The Dutch startup/grownup Bambooder has been working on biobased alternatives for traditional fossil fuel produced composites since 2014.
Bambooder‘s founder Marc Bokeloh and co-founder Dr.Ir.Ing. Almer van der Stoel developed a patented technology to mechanically extract bamboo fibers and produce semi-finished products for high-performance composite applications.
- The Dutch company Bambooder is bringing an easily renewable material – bamboo fibers – to the field of high-performance composite applications competing with materials such as steel or glass fibers
- Bambooder has developed a patented technology to mechanically extract bamboo fibers and produce semi-finished products for high-performance composite applications
- Bambooder’s main product are technical yarns made of long bamboo fibers (12-50cm) for continuous fiber 3D printing, UD tapes or textiles
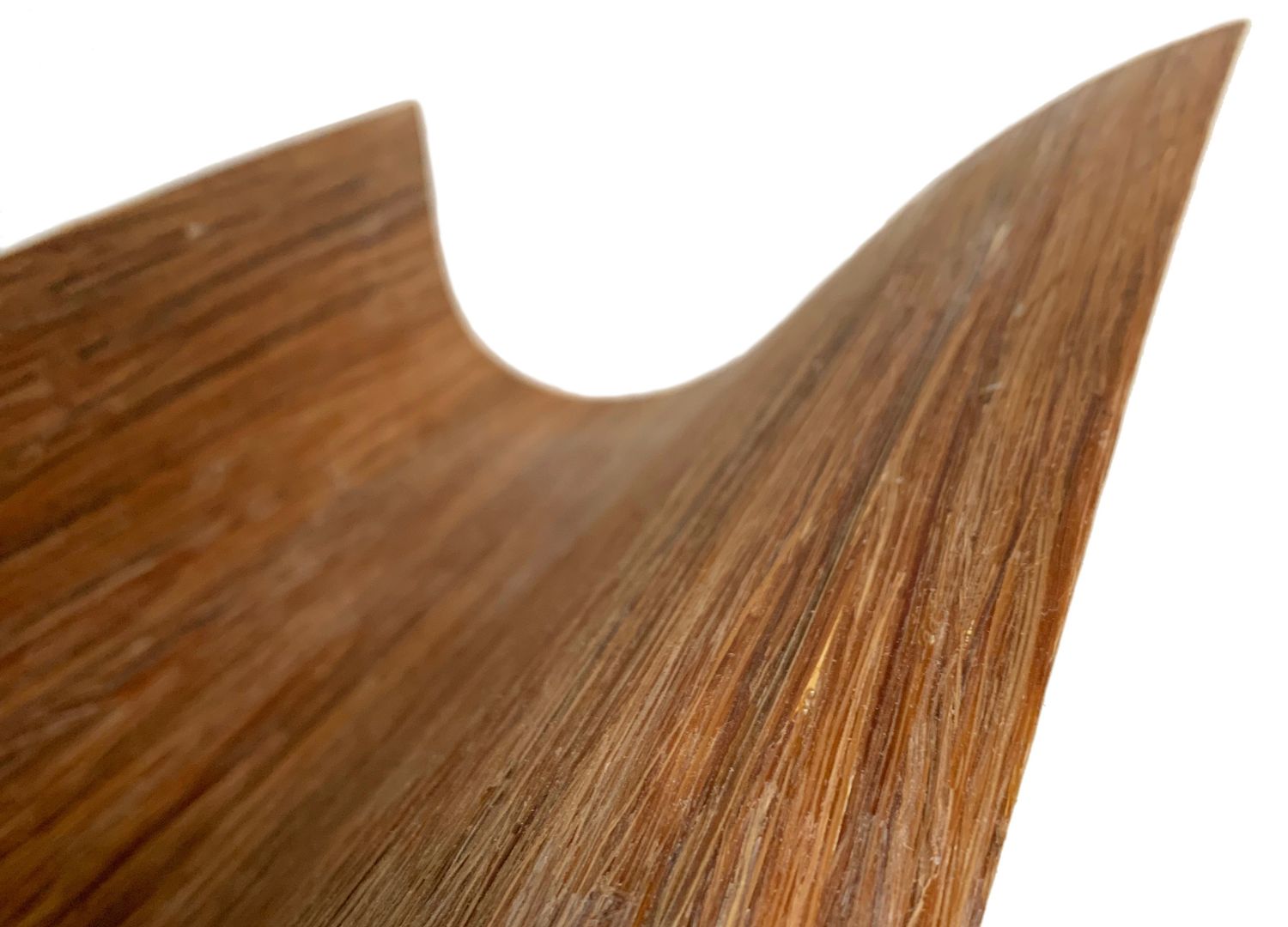
Their main products are technical yarns made of long bamboo fibers (12-50cm) for continuous fiber 3D printing, UD tapes or textiles. All side streams are used to produce short fibers suitable for non-woven mats, injection moulding compounds or 3D printing filaments.
Such materials can compete with steel, aluminium, carbon, glass, and other natural fibers depending on the required properties. Bamboo has the advantage that it is light, strong, and sustainable. The fast growth of bamboo results not only in higher CO2 uptake than other plants, but also in a significantly higher fiber yield than other natural fibers.
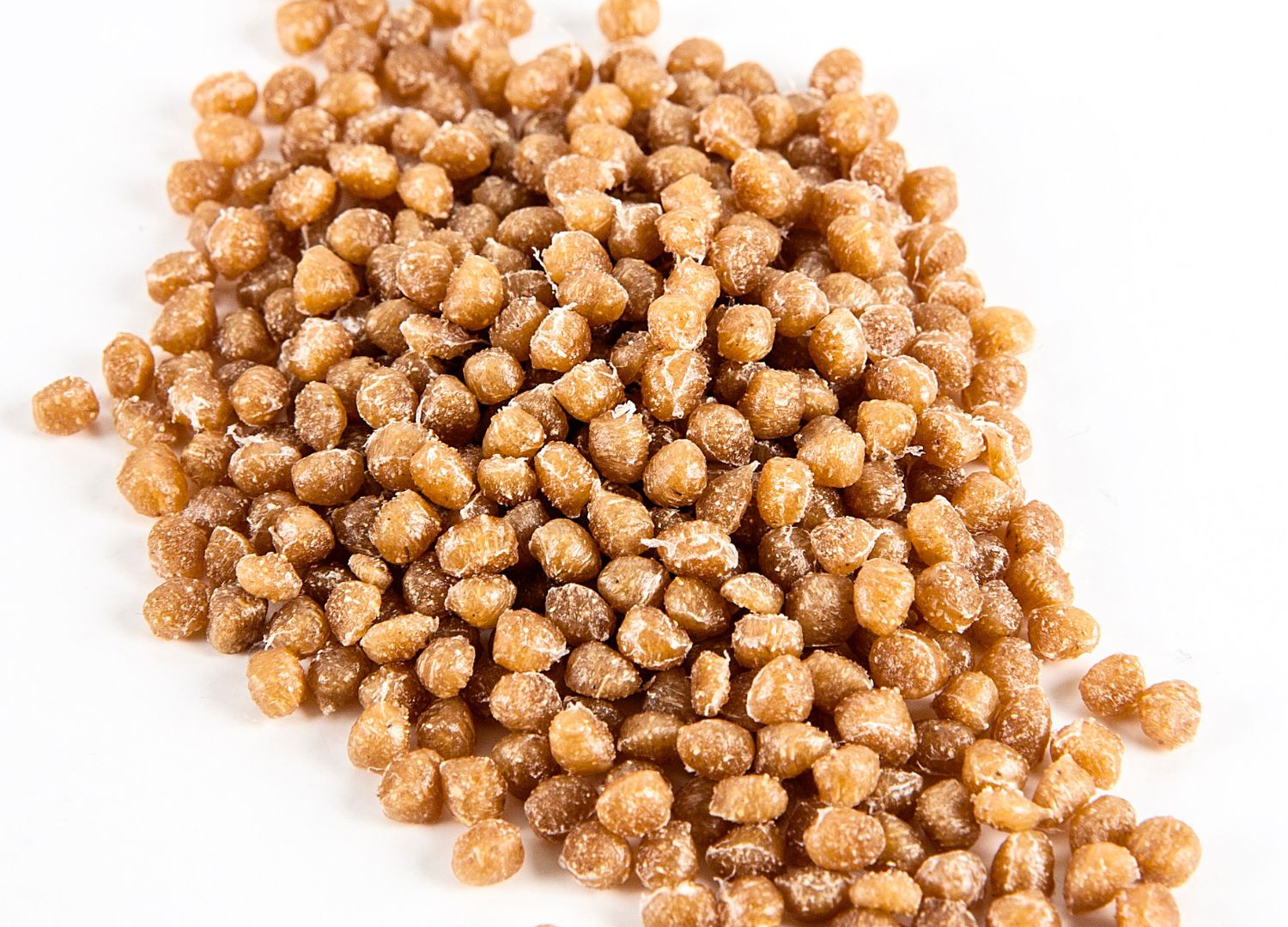
Applications vary depending on the specific material derived from Bambooder patented processes. Short fibers filament combined with PLA can be 3D-printed to shape decorative objects. Bamboo cork sandwich panels, made of two outer layers of non-woven short fiber mats combined with an inner layer of cork, offer heat insulation, sound absorption and function as an electric insulator.
Mats derived from short bamboo fibers are a sustainable alternative for non-woven glass fiber mats and can be applied through techniques such as hand lamination, thermoforming, and vacuum infusion.
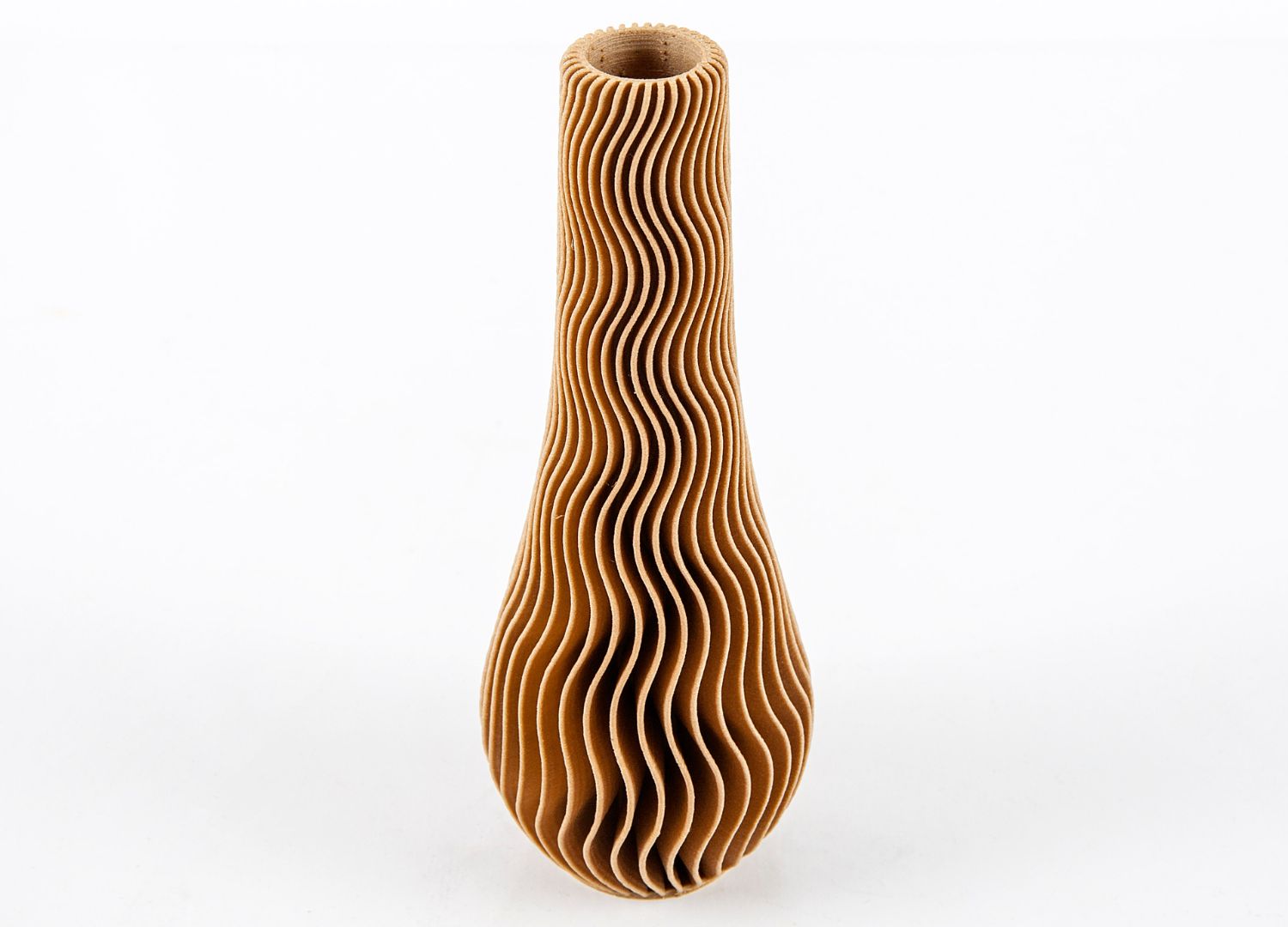
Long bamboo fibers are used to manufacture a technical yarn that can be used for continuous fiber 3D printing filaments, unidirectional tapes and in textiles as sustainable replacement of carbon and glass fiber. Because UD tapes give stiffness in one direction, the stiffness of products can be influenced by stacking UD tapes in different directions. As a result, UD tapes give the component strength exactly where it is needed and components can carry more load even with thinner walls and no ribs.
Being virtually a highly sustainable replacement of glass and carbon fibers, these products can be used in many industries and design areas: transportation, sports, energy, design, building & construction sectors. Lightweight elements in trains, trams, metro cars, and buses; surf and skateboards, skis and bikes – all of these products could well use bamboo-based fibers, as well as automotive, aeronautics, furniture and lighting design.
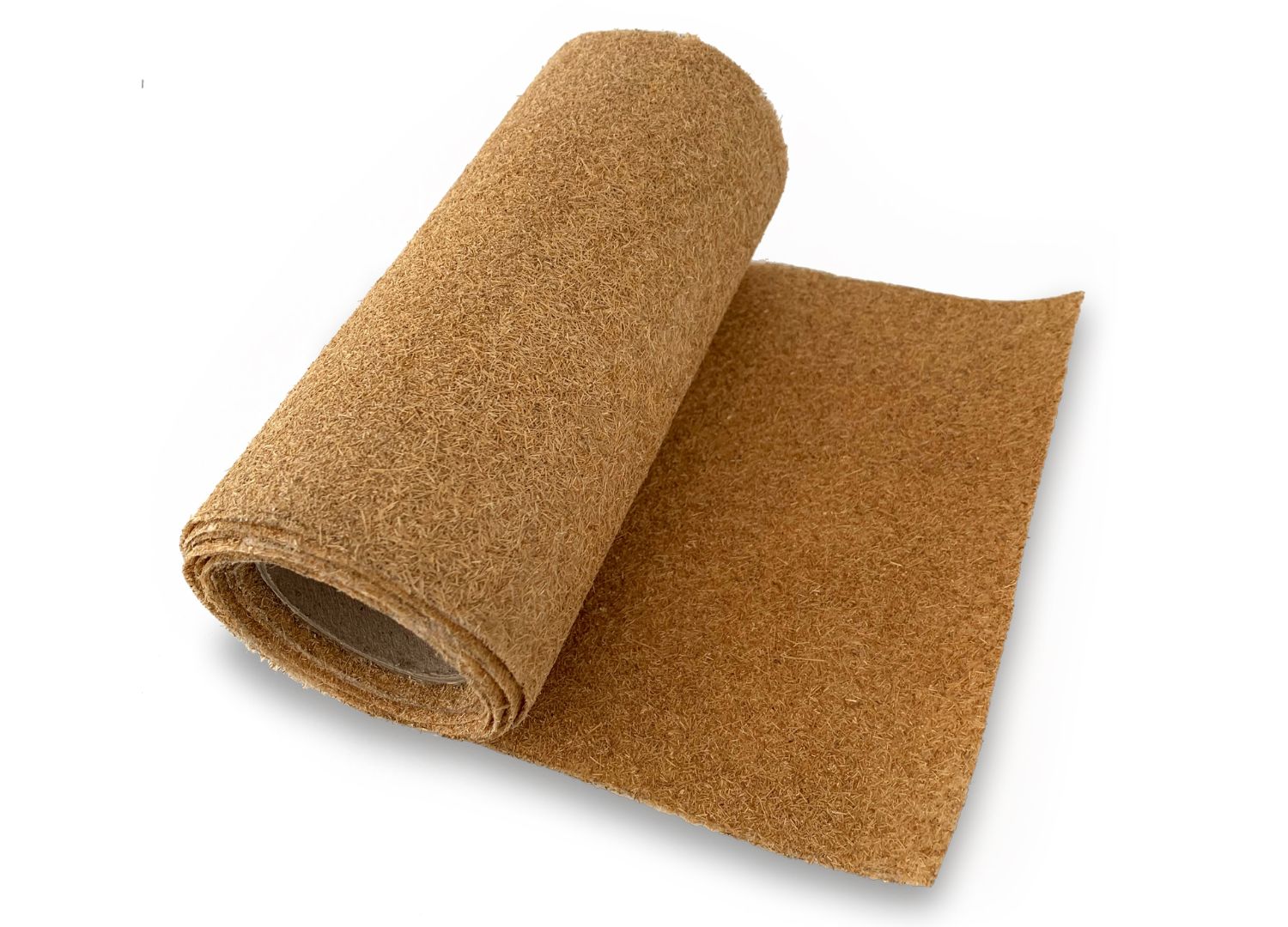
Given their versatility in application and diversity in format, materials derived from the Bambooder patent have few downsides when it comes to standard applications. However, these are not a replacement for every material in every condition. Moderate UV, scratch, chemical and weather resistance do not make them ideal solutions for outdoor elements and chemically or mechanically stressed applications.